

This in turn can be costly in terms of raw material, mould material, energy and set-up time. As a result the process is a ‘black art’ and can rely heavily on previous knowledge and operator experience. This manufacturing process is complex with variables such as magnitude of pressure, air flow, preform temperature and stretch-rod velocity all influencing the final bottle thickness and mechanical properties. The pressure inflation occurs in two stages pre-blow (6-10 bar) to form the majority of the bottle shape and final blow (>25 bar) to form the final bottle shape and bottle details. The manufacturing process that has been developed to form the containers is the injection stretch blow moulding (ISBM) process where injection moulded PET preforms are reheated above the glass transition temperature Tg using infrared radiation, placed into a suitable mould and then formed using a combination of linear stretching and air pressure inflation. This is due to its clarity, light weight, strength, recyclability and barrier properties, not to mention the relatively large process window available to the manufacturer.

Poly (ethylene terephthalate) (PET) is the dominant material for the manufacture of thin-walled containers.
#BOTTLE PREFORM FULL#
Investigation into the effect on deformation mode, strain rate and final bottle shape provide a basis for full understanding of the process optimisation and therefore how the process inputs may aid development of the preferred optimised container. The unprecedented experimental analysis reveals that the deformation behaviour varies considerably with contrasting process input parameters. Process outputs cavity pressure and stretch-rod force were recorded using at instrumented stretch-rod and preform surface strain mapping was determined using a combination of a unique patterning procedure and high speed stereoscopic digital image correlation.
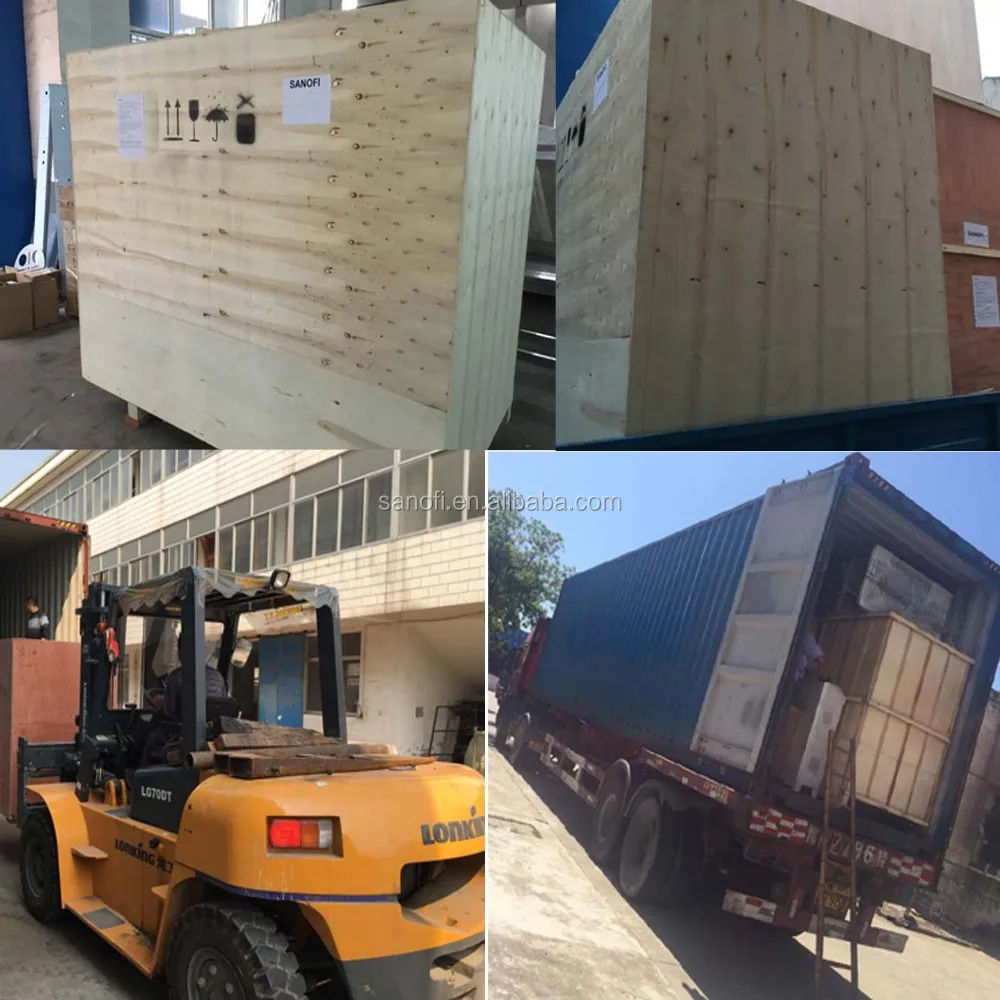
Removing the bottle mould and performing free-stretch-blow (FSB) experiments revealed insight into the bottle forming characteristics at various preform temperatures and blowing rates. The processes required to form PET bottles are complicated and extensive any development in understanding the nature of material deformation can potentially improve the bottle optimisation process. This paper highlights for the first time a full comprehension of the deformation procedure during the injection stretch blow moulding (ISBM) process of poly(ethylene terephthalate) (PET) containers, namely thin-walled rigid bottles.
